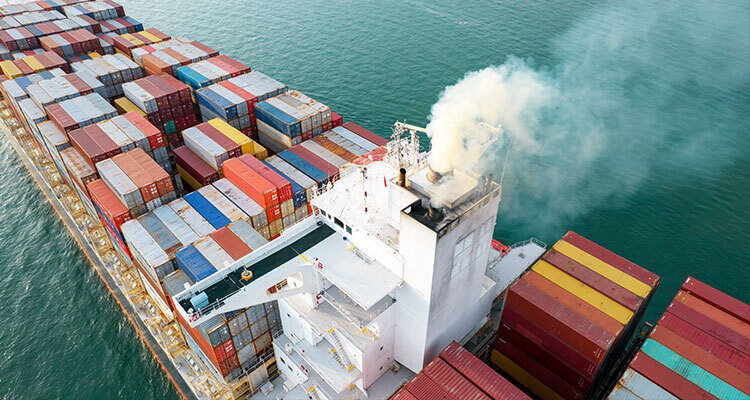
Hydrogen-on-demand creates a practical route for global shipping
Regulatory entities worldwide are mandating environmental changes in the shipping industry, putting a sharper focus on shipping’s role in global carbon production. Shipping operators are being tasked with greater sustainability and lowering pollution production, meeting a 40 percent cut in carbon emissions by 2030 and, at minimum, 50 percent by 2050. New guidelines and policies are setting a monumentally high bar – underscoring the critical nature of reducing carbon impact ahead of strict deadlines for emissions reduction.
At the same time, many market sectors can be slow to embrace new, cleaner technology, particularly those relying on costly heavy equipment as a primary business asset. The massive change ahead represents genuine transformation for an industry that took 200 years to evolve from wooden to steel boats. While hydrogen energy is proving highly suitable as a clean fuel for the shipping industry, what will it really take for ship operators to embrace hydrogen as an energy source for cleaner propulsion? And how do shipbuilders weigh the risk of adopting new technologies today versus the risk of waiting to adopt even greener fuel solutions?
All these considerations indicate that the conversion to cleaner fuels is about much more than simply the fuel itself. Solutions must offer long-term strategic value to shipbuilders and maritime professionals, providing a truly viable path to mandated decarbonization. Hydrogen-on-demand aligns well – today and for the future – tapping into existing methanol infrastructure to remove obstacles, reduce complexity, generate immediate value, and create a flexible path to accelerating decarbonization efforts.
Hydrogen-on-demand: convenient and available
Stored hydrogen requires high pressure or cryogenics, complexities that stand between the global shipping industry and its wholehearted embrace of hydrogen as fuel. But hydrogen-on-demand relies on methanol as a hydrogen carrier feedstock. This approach solves the inherent complexities, cost, and logistics of onboard hydrogen as a clean source of ship energy. Methanol-to-hydrogen, or M2H2, is deployable today and addresses the difficulties of hydrogen transportation and storage, whether deployed onboard vessels or portside.
Methanol is a low-toxicity substance common to the marine industry in portside and on-vessel applications. This existing methanol infrastructure removes risk and costs while increasing convenience and fostering overall comfort with change. It’s versatile, familiar to marine professionals, and well established, with wide accessibility in seaports worldwide and approval from the International Maritime Organization (IMO) for bunkering and various marine uses. In addition to its capacity to be refined into highly pure hydrogen, its handling requirements are straightforward and akin to other fuel types. Methanol is biodegradable, dissolves in water, and stays in a liquid state at normal temperatures without high-pressure tanks or cryogenics.
In an M2H2 system, high-purity hydrogen is generated on demand through the methanol-reforming process. There is no need for dangerous, big-footprint storage of highly pressurized hydrogen or complex cryogenic liquid hydrogen storage. And when consumed by a fuel cell, its only additional output is pure water.
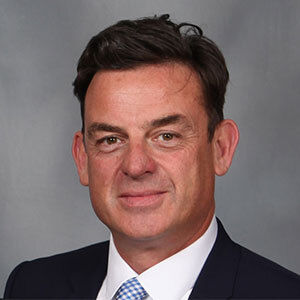
Portside potential
Methanol-to-hydrogen systems can also readily cater to portside applications for both general port facilities and docked ships. For instance, M2H2 container systems can be easily relocated to provide power for various port operations. Similar to the port’s existing diesel systems, these containerized systems can be deployed to deliver power whenever necessary. What sets them apart is their exceptional cleanliness and quiet operation, eliminating the noise and pollution typically associated with diesel systems. The containerized system, along with its reformers and interconnected PEM fuel cells, can be conveniently moved based on the docking location of larger cargo vessels.
When a ship enters a port, the operators usually prefer to connect to shore power instead of running the ship’s diesel systems. However, port facilities and their power grids often face significant weather-related disruptions, forcing incoming ships to rely on their onboard engines while docked. Power supply becomes crucial to maintain the ship’s facilities and cater to the requirements of their cargo, like specific storage conditions or refrigeration.
It is anticipated that many larger ships will transition to methanol internal combustion engines, using methanol itself as a fuel rather than fuel cells. As a result, ports will need to bunker significant amounts of methanol to address the refueling of these ships. With M2H2 technology, ports can achieve a dual benefit from their methanol resources and generate hydrogen portside. In ports with considerably volatile weather conditions,
like those in Houston, the technology becomes particularly appealing. The intricate nature of such port facilities, serving as transit nodes with unique specializations, geographical challenges, and services, may also require the integration of electric vehicles (EVs) as part of their operations. Functioning much like small cities, these port environments are actively working towards electrifying essential equipment such as cranes or drayage trucks, further highlighting the advantages of the M2H2/PEM fuel cell combination.
Net Zero is a journey
With its unchanging complexities, stored hydrogen solutions just won’t work for
clean shipping and propulsion. The answer lies in developing access beyond stored hydrogen – tapping into a proven reforming process and M2H2 systems generating hydrogen on demand.
Most importantly, shipping operators do not need to wait for the availability of green methanol to make meaningful progress toward their decarbonization goals. Methanol-to-hydrogen reforming can use gray, green, or a mixture of both – deployable today and only getting greener as more sustainable methanol options become a reality. As new fuels become available, vessels already outfitted with M2H2 reforming technology will be ahead of the pack and comfortably on course to avoid carbon levies that are beginning now. Mandates for reduced emissions are on the horizon; hydrogen-on-demand is here now.
For a list of the sources used in this article, please contact the editor.
Bryan Reid
www.rixindustries.com
Bryan Reid is Chief Sales Officer at RIX Industries. With a rich history in rugged design and engineering, RIX is responsive and nimble, partnering effectively to deliver technology insight. The company invests in customer relationships just as it invests in developing a culture of inspired design and ambitious engineering – delivering benefits not just products. From design to delivery to lifetime support, RIX offers unmatched versatility and real-world expertise that taps into its unique engineering talent and proud heritage.