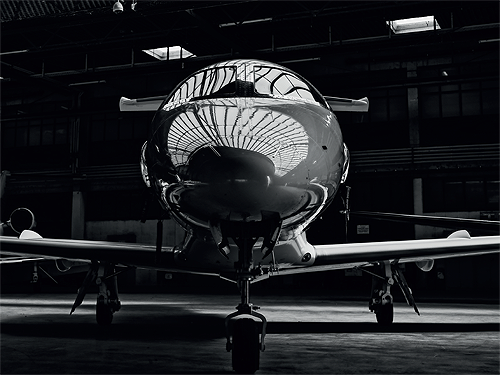
Turbulence ahead
Navigating rapid demand changes in the A&D industry. By Kourosh Samini
AAerospace and defense (A&D) is a broad sector encompassing a raft of organizations, each facing different but momentous challenges in navigating the current crisis. Civil aerospace has been especially badly hit by the pandemic, with many airlines now running at only around 20 per cent capacity as a result. The arrival of the vaccine has the potential to help restore air travel to pre-Covid levels but airlines aren’t expecting to see a significant boost in passenger numbers in the near future at least.
This drop off has had a knock-on effect on aerospace manufacturers who have seen demand for aircraft drying up. In the UK, aircraft manufacturers received just 13 orders in July and August 2020 and none in September. This figure compares with 152 during the same period in 2019. At the end of October 2020, it was being reported that 12,000 UK jobs in aerospace had either been lost or were at risk because of the Covid-19 pandemic. Defense has been doing better thanks to funding from government ministries, but even here reductions in government budgets may impact manufacturers over the longer-term.
Across both industries, there is an important people dimension, with many employees unable to carry out factory work because they are self-isolating, sick, or concerned about risks. The fact that vaccines are now being rolled out is, of course, welcome news for the sector, but a new approach will still be required by all the stakeholders involved if the A&D industry is to start returning to its previous strength any time soon.
The immediate challenges
Moving forward, it is inevitably going to be a challenge for all A&D firms to get a handle on demand. Forecasting how demand fluctuations will impact airlines and aircraft manufacturers will be very difficult; the industry is facing an unprecedented environment so historical forecasting will be of little value and traditional sequential forecasting is just too slow.
As a result, many manufacturers, whether they supply into the civil sector or defense, will cut optional capital spending to support operational continuity and they may also reduce expenditure on non-essential projects until demand picks up. This strategy may well work for larger manufacturers, but tier one and tier two suppliers will struggle as they lack the financial power to bounce back.
These supplier businesses will likely end up being the bottleneck from the financial and operational standpoint so they will take a greater hit which will disrupt the whole supply chain. This turbulence will affect civil aerospace in particular, while defense will remain cushioned from the worst impacts because it will be able to turn to government support to protect the supply chain.
Planning further ahead
Over the longer-term, companies are looking to develop a more flexible supply chain that allows them to move to an alternative supplier if one link in the existing chain fails. We are seeing a huge shift to manufacturers wanting to put in place an alternative supply chain and those manufacturers that fail to do so will surely feel the longer-term impact severely.
In the civil sector the old normal seems elusive. With few able to predict for certain whether we will ever get back to anything like the demand levels of the past, it is high time for a new approach to help the industry get back on its feet.
Looking for a better way forward
Whether civil or defense though, manufacturers need to ask: how do we get a stronger real-time awareness of the supply chain? They must understand, for example, which locations have hardly been affected by Covid-19 as well as the places where there has been a heavy impact.
Manufacturers also need to be aware of how they can gain access to alternative suppliers. They must keep lines of communication with customers and suppliers open. That’s especially key with the defense industry because if they fail to do so they could end up incurring huge penalties.
There is now a need to move away from the sequential planning and manual-focused approach that many have relied on historically to move to a more agile planning methodology. Doing this will help manufacturers mitigate risk going forward.
Preparing for recovery – the keys steps
In terms of defense, the end customer is the government so contracts are likely to be program-based and therefore will have specific systems, data, and operational processes in place. For example, part numbers that can be specifically introduced for the duration of a program helping to track parts. Any changes in circumstances, to do with a part for instance, will need to be communicated across the supply chain. Lack of transparency across the extended supply network can result in a failure to fulfil an order by any contractor which will have a knock-on effect on the entire chain, leading to conflicting priorities where different contractors bid for different projects.
If manufacturers don’t address this issue, they will overrun budgets and be forced to ask for more money and as a result they are likely to be penalized by the government.
On the other hand, civil manufacturers have commercial agreements with private companies. These businesses will need to look into alternative suppliers, real-time visibility and achieve real-time situational awareness across the chain. Ultimately, A&D manufacturers don’t have the power to stop the disruption, but what they can and must do is find and prioritize ways of mitigating the risk.
The key role of concurrent planning
The best way to do this is by adopting a concurrent planning technique. Concurrent planning is the process of making and managing unified plans across multiple time horizons, business processes and organizational boundaries at the same time. It synchronizes data, processes and people to collapse decision-making time, break down organizational boundaries and dynamically balance the end-to-end network. If one person makes a change, everyone else instantly understands the impact on themselves, their team and the organization.
Whether civil or defense, this can help manufacturers to reveal supply chain failures by modelling their entire supply chain and creating a digital twin of it. They can then reduce supply chain risk by providing full visibility through this concurrent technique throughout the entire extended supply chain network.
Any potential disruption can be modelled to provide the ability to assess the alternative risk mitigation scenarios and all this can be done in real-time. New kinds of approaches such as this will certainly be necessary to ensure a bright future lies ahead for the sector.
Kourosh Samini is Senior Industry Principal at Kinaxis. Kinaxis® delivers the agility to make fast, confident decisions across integrated business planning and the digital supply chain. People can plan better, live better and change the world. Trusted by innovative brands, it combines human intelligence with AI and concurrent planning to help companies plan for any future, monitor risks and opportunities and respond at the pace of change.
www.kinaxis.com