Benjamin Ting, Chief Commercial Officer of Echion Technologies explores the emerging battery chemistries that could positively impact industry operations
Industries around the world are taking steps to achieve net-zero emissions by 2050 and the UK transportation and logistics sector is one of the industries leading the charge, and setting an example that other industries should note. Electric forklifts, pallet trucks, and stackers are already commonplace in UK warehouses. However, while within warehouses, electric vehicles are relatively commonplace, there are limitations on the vehicles’ capabilities due to outdated battery technologies. In a 24/7 industry like logistics, time spent charging vehicles is money lost, but there are emerging innovative chemistries that could simultaneously improve current vehicle efficiencies, electrify more vehicles within operator fleets, and accelerate the transition to a low-carbon industry.
Most warehouses, ports and freight terminals in the UK, to some extent, utilize a percentage of electric vehicles within operations. Different vehicles require different types of batteries and in general, smaller electric vehicles used in warehouses, such as forklifts, are powered by either lead-acid batteries or lithium-ion (li-ion) batteries. Both types of battery have their benefits, with lead-acid batteries requiring less complex monitoring and management systems than li-ion batteries, but li-ion batteries having significantly faster charging capabilities. Lead-acid batteries are also much bigger in size and weight than li-ion batteries, and although this can be paradoxically advantageous if the battery also functions as ballast weight, this is not the case for most other vehicle types where the higher energy density of li-ion cells is preferred. Finally, lead-acid batteries have a lower up-front cost, but li-ion batteries have a significantly longer cycle-life, meaning they require replacement less regularly.
Li-ion is the most common battery type in modern passenger electric vehicles and attempts to scale up this technology for usage in heavy duty vehicles, such as lorries, trains and large construction machinery are well underway. However, in these new use cases, limitations have been identified.
Any time a vehicle is having to charge, it is simultaneously losing money by not being in operation and costing money through energy consumption. While li-ion batteries can charge faster than lead-acid cells, it can still take up to two hours to fully charge a li-ion forklift battery. When this technology is scaled up for use on a heavy-duty vehicle, vehicle mass or volume limits are reached and a reduction in vehicle efficiency is observed. If the limits of the vehicle are not a problem, then typically the size of the battery requires prohibitively expensive charging infrastructure.
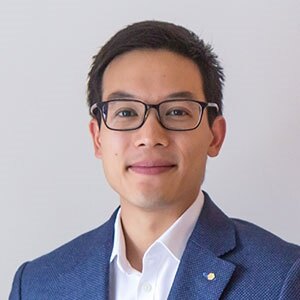
While lead-acid batteries are seen as the battery of choice for parts of the industry, their size and weight, partnered with their relatively low cycle life make them less likely to feature in future industrial vehicle electrification. The cost of li-ion batteries has also dropped which is attracting more interest in using this technology, but not all li-ion batteries are created the same. By exploring the different components of the batteries themselves, marked improvements can be made in terms of speed of charging, lifecycle, safety, and in the long term – cost.
Li-ion batteries are made up of four main parts: the cathode, anode, separator, and electrolyte. The anode is what receives and stores electrodes during battery charging, and it has an important role to play in cell safety, energy density and cycle life. When it comes to improving the charge rate and thus, the productivity of battery electric equipment, the anode is arguably the component with the most potential to unlock improvements for vehicles across the industry.
The li-ion batteries used in most vehicles in the industry are equipped with graphite-based anode materials. These materials offer high energy densities and can safely and repeatedly charge to around 80 percent capacity in 20-to-60 minutes. A vehicle having to spend up to an hour in down time is not well suited to the needs of a 24/7 industry and ultimately means that more vehicles need to be added to fleets to maintain operational output. Furthermore, when operated at a high rate in extreme low or high temperature environments, graphite anode batteries come with safety and longevity concerns.
An alternative material is lithium titanate oxides, commonly referred to as LTO. Lithium titanate batteries can easily charge to 80 percent in less than ten minutes and offer high power across a cycle-life of over 10,000 cycles. Whilst their upfront price is higher than a graphite-based li-ion battery, the longer cycle life means they have a lower total cost of ownership. The shortcomings of li-ion cells using LTO anodes center around their low energy density, especially volumetrically. This means that you will likely run out of space before you can fit the required capacity of batteries to operate as desired. Whilst this low energy density can be sometimes offset by fast charging, it makes LTO an unviable option for the full range of vehicles used across the industry, especially those which require a lot
of energy between charging.
A slightly lesser-known material called niobium has now been identified for its potential to significantly improve charge time, cycle life, energy density and safety of li-ion batteries. At Echion Technologies, we engineer a niobium-based anode material called XNO®. Cell testing of li-ion batteries containing XNO® has shown that niobium-based anodes can charge as fast as LTO, last as many cycles as LTO and can be as safe as LTO. Most importantly, XNO® cells can achieve up to 180 percent of the energy density of LTO which allows operators to access a battery that performs like LTO, but with the energy density required to electrify significantly more vehicles within fleets.
Niobium as a mineral is neither rare nor scarce, and it doesn’t require intensive mining practices to access it. Independent research revealed that it also has a carbon footprint 2.5 times lower than LTO at cell level, meaning industry operators can enjoy the safest, fastest charging, most environmentally friendly batteries available on the market today.
The industry has been utilizing electric vehicles within its fleets for long periods of time and deserves recognition for progressing towards achieving the required net-zero emissions by 2050. However, by utilizing the latest battery technologies as opposed to relying upon the batteries commonly used today, the industry could simultaneously improve its productivity, reach its emissions reductions targets, and save money in the long-term. I call for the industry to pragmatically explore the benefits that new anode chemistries bring and be the first mover to trial them in operations.
For a list of the sources used in this article, please contact the editor.
Benjamin Ting
Echion is the world’s leading supplier of niobium-based anode materials, providing advanced technology to solve some of the biggest challenges in the space of climate change and electrification. Its product, the Echion XNO® anode material, enables some of the world’s largest transportation companies to access sustainable batteries with outstanding safety, longevity, and fast-charging capability.